連載記事
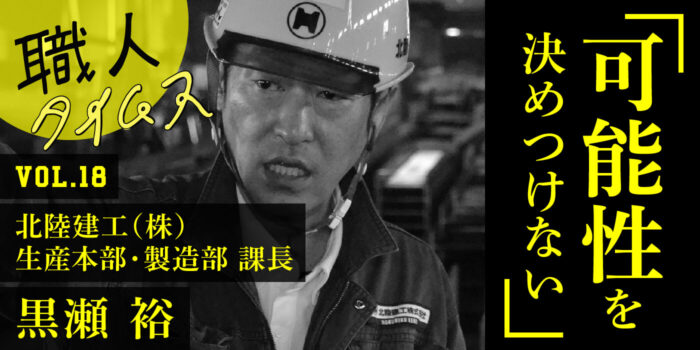
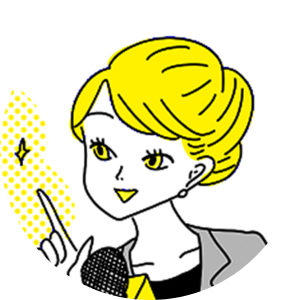
ラボ
まずは、黒瀬さんが北陸建工に入社されたキッカケを教えてください!
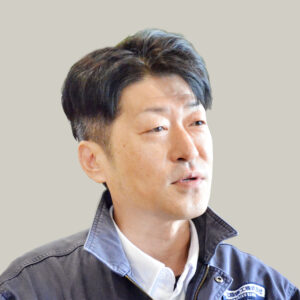
黒瀬さん
高卒で入社して今年で24年目、もうすぐ四半世紀ですね(笑)。工業高校に進学した事も将来の就職先を考えて……とかではなく、ただ単純に吹奏楽部が強かったからです。
進路を決めた当時は今と違って就職氷河期で企業をどこでも選べる時代でありませんでした。学校の進路相談に行った時、残っていた2社のうちの1社が北陸建工でした。
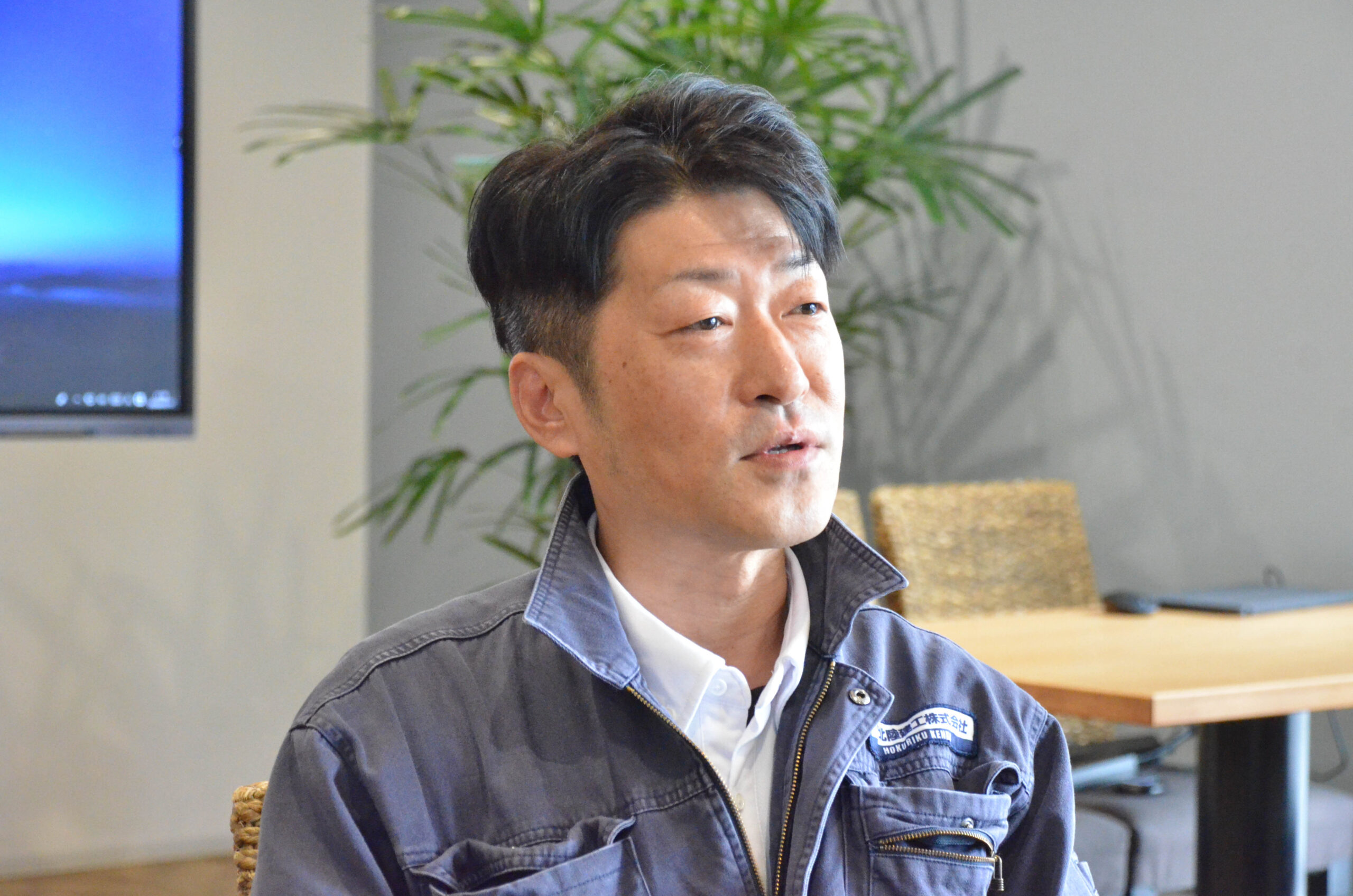
就職する際2社で迷った結果、給料の高い方を選んだと話す黒瀬さん。
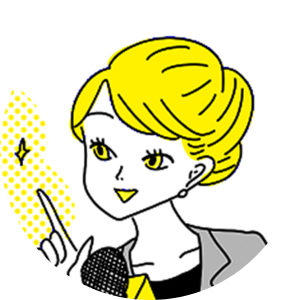
ラボ
その時の北陸建工さんにどんな印象を持ちましたか??
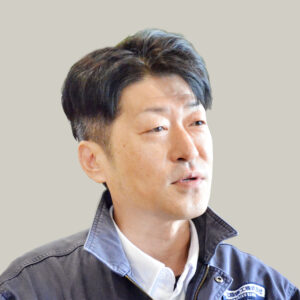
黒瀬さん
その時は“町工場”の印象でしたね。今みたいにCMが流れたり、沢山の人に知ってもらっている企業という感じはしなかったですね。入社式はトレーナーにジーパンで行った記憶があります(笑)。
今は社員も130名を超えていますが、当時は50名いるかいないかくらいでした。地元の会社だけど僕自身も全く知らなくて、後に電気系の会社を経営している叔父に聞くと、「いろんなものを鉄で作っている会社だよ。いい会社に入ったね」と言われて、「そうなんだ!」と思ったくらいでした。
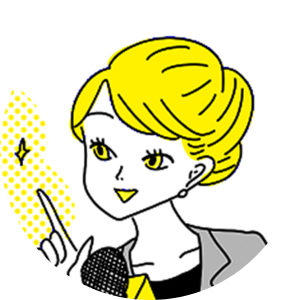
ラボ
入社されてから黒瀬さんは、どんなお仕事をされているのでしょうか?
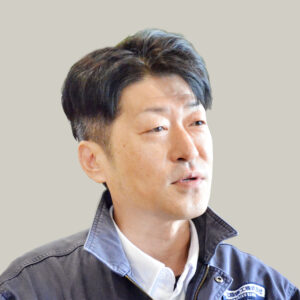
黒瀬さん
入社してからの10年ほどは、ひたすら鉄塔ばかり作っていました。それから合成床版、制震デバイス、橋梁、鋼製鳥居、鋼製階段、特殊鉄骨など様々な製品や物件の製造を経験し、現在に至ります。
当社は円柱の照明鉄塔、無線鉄塔では間違いなく国内シェアNo.1です。地元富山のアルペンスタジアム、県総合陸上競技場だけでなく、神宮球場や甲子園、MAZDA ZOOM ZOOMスタジアム、花園ラグビー場の照明鉄塔も手掛けています。
これまで僕が携わった鉄塔は1000基以上。高速道路から見える円柱鉄塔は、ほぼ僕が作ったと言っても言い過ぎではないと思います(笑)。
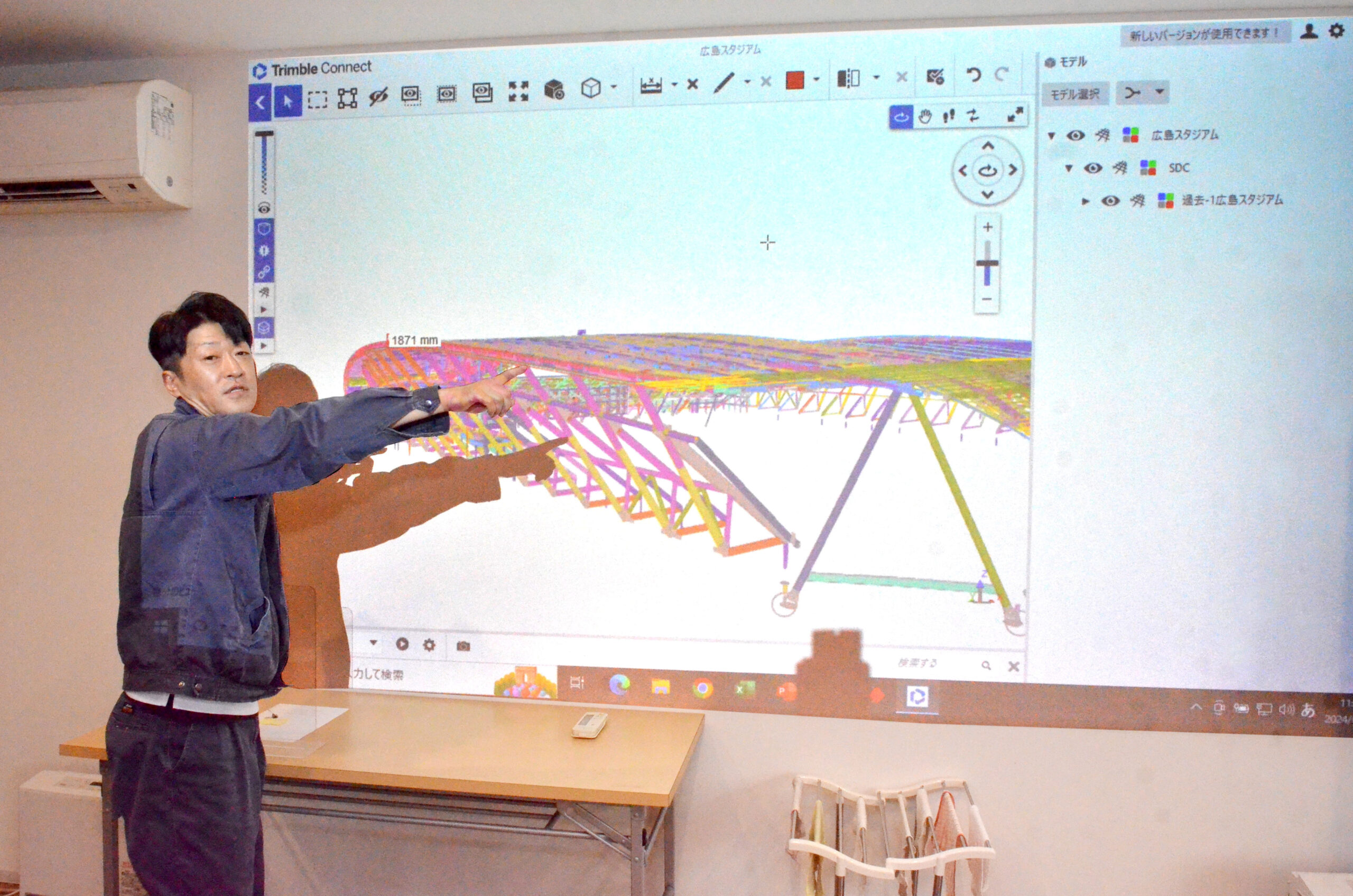
スタジアムのBIMデータを特別に見せていただきました
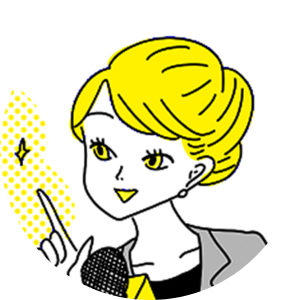
ラボ
ものスゴい実績ですね! 入社されて24年、黒瀬さんにとってのターニングポイントはありましたか??
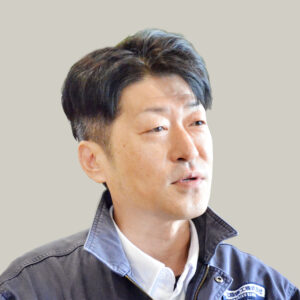
黒瀬さん
最初は鉄に興味が持てなくて、淡々と仕事をこなしていました。若かったし、遅刻もいっぱいしましたね(苦笑)。
当時の仕事は鉄板を切る、曲げる、穴を開けるといった“一次加工”と呼ばれる前加工ばかりで組立や溶接に携われず、できたとしても手元と呼ばれるお手伝いだけだったので、全くやりがいを見出せず…。
そんな時に、たまたま上司が長期離脱することになって、大阪の住之江競艇場の照明鉄塔を任せてもらう機会があったんです。入社して5〜6年目の出来事でした。
そこで、初めて前加工から組立て、溶接まで全てを自分でやってみて、「今までやっていた仕事はこういうことだったのか!」と全部が繋がりました。
鉄板一枚あれば形にして、色を塗って、運んで、据え付け管理までやるという北陸建工の一貫生産のスゴさ、そして仕事の面白さに気づいたのは、まさにその時でした。
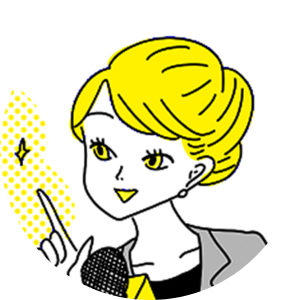
ラボ
あんなに大きな鉄塔を、実際にどうやって作るんですか???
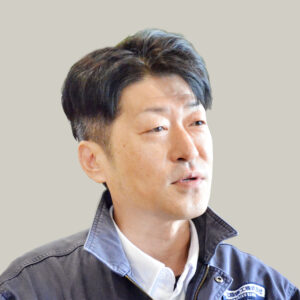
黒瀬さん
12mの鉄板をプレス機に入れて、まず半円を作ります。出来た半円と半円をくっつけて、溶接するとパイプになる。それを大きなものから順番に並べるように寝かせて30m、40mに組んでいきます。
特段問題がなければ、組んだものをまたバラして(分解)、塗装を施しトラックで輸送する。ここまでが、自社工場で可能な作業になります。
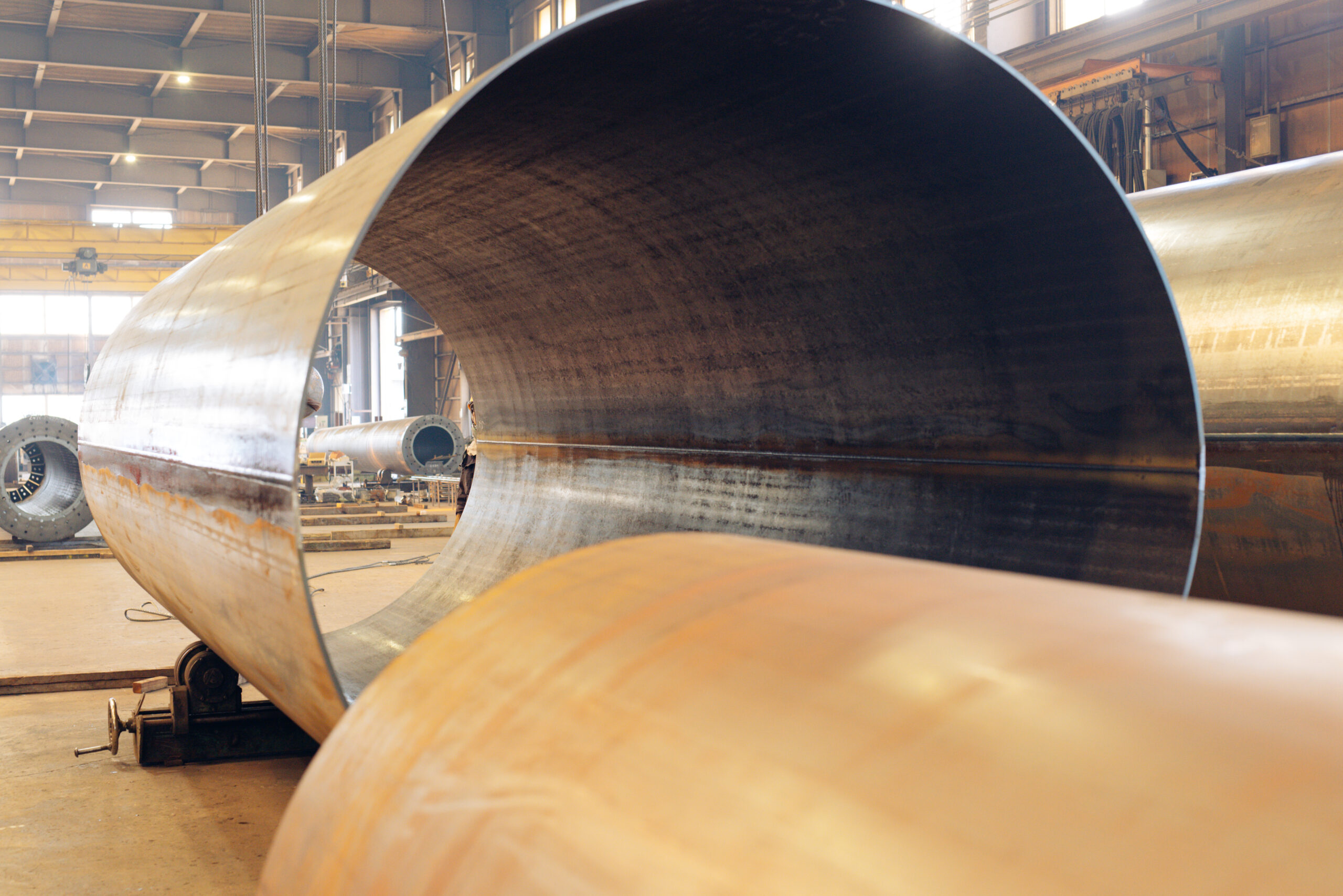
鉄塔をつくるために必要な溶接されたパイプ
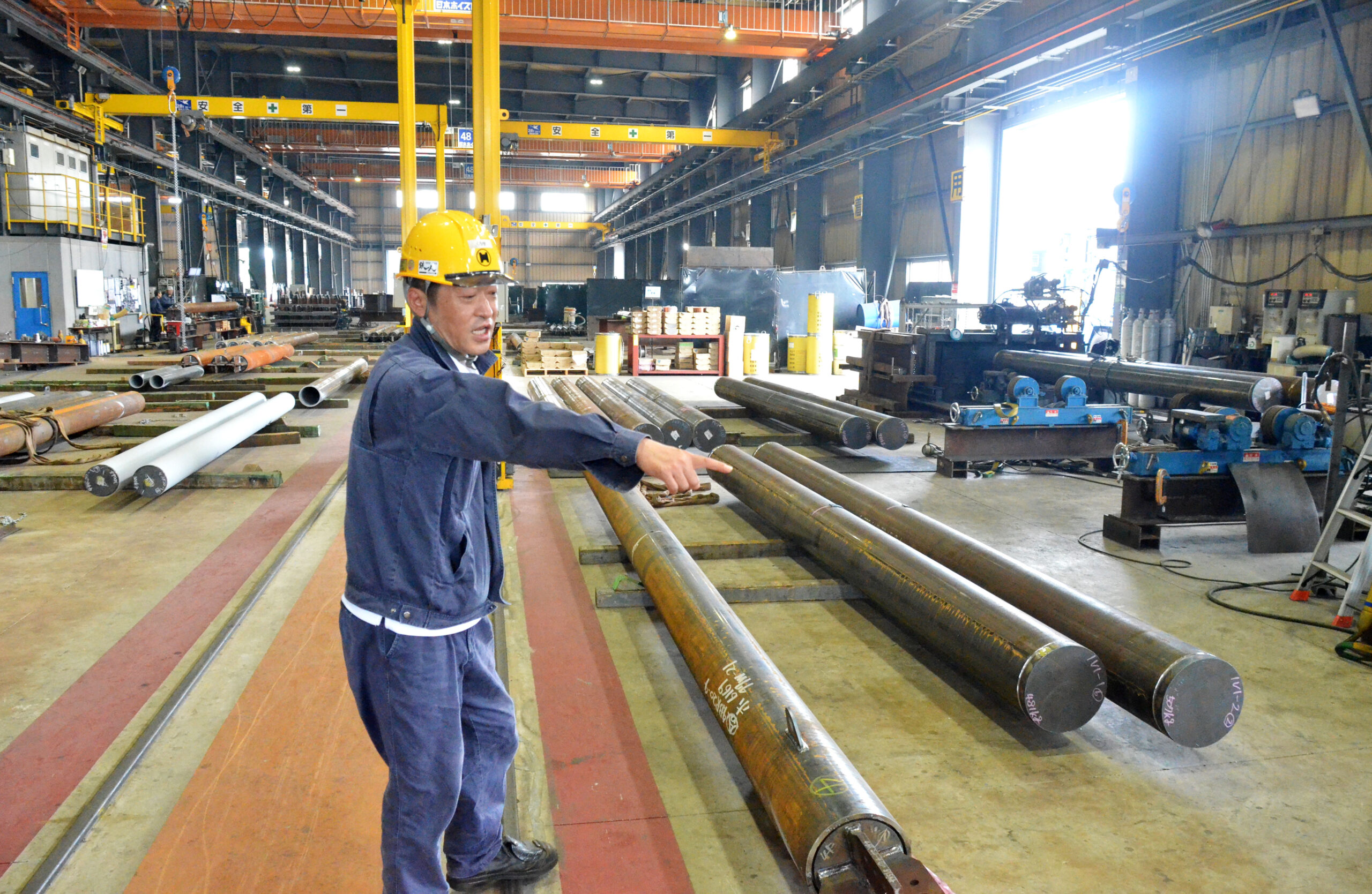
黒瀬さんに工場を案内してもらいました
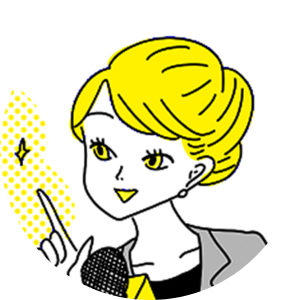
ラボ
一度出来上がったものを運ぶために、バラすんですか!??
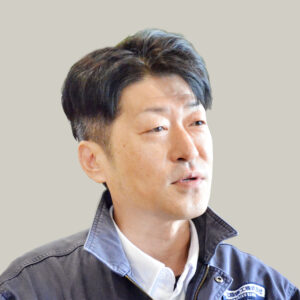
黒瀬さん
そうなんです!30m〜40m級の製品を運ぶ術がないので、設計段階で輸送できる大きさに区切ってあるんです。また、お客様や現場に間違いのない物をお届けする為、工場で完成品に近い形まで作ります。
大組みや仮組みといって、現場施工のリハーサルのような作業です。これをする事によって製品精度が確保され、現場トラブルを防ぎ、スムーズに現場施工出来るようになります。
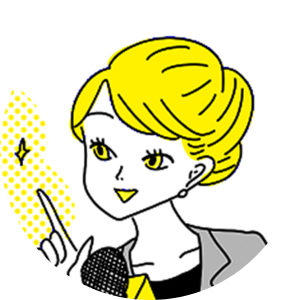
ラボ
施工から運搬、設置までを全て北陸建工さんが手掛けられるんですね!
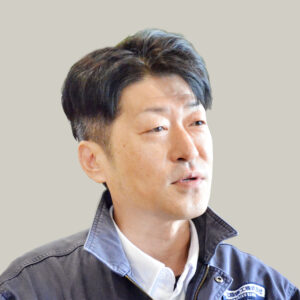
黒瀬さん
勿論、協力業者の力もお借りしますが、施工管理として必ず当社の社員が現場に行きます。製造から現場での設置、据え付け管理まで全て行うのが当社の強みです。
鉄骨製造の仕事をよく部品を組み立てるだけのプラモデルと例えられますが、当社の製品や物件はそうではなく、設計図に沿って完成形をイメージしながら部品の製造から作り方を考える。そこからスタートになります。
お客様から来た設計図面を社内で検討し揉んで、「こんな形はどうでしょう?」とこちらの意見として返す。それを納得いただけるまで繰り返し、設計部で製造用の図面に落とし込むという流れです。
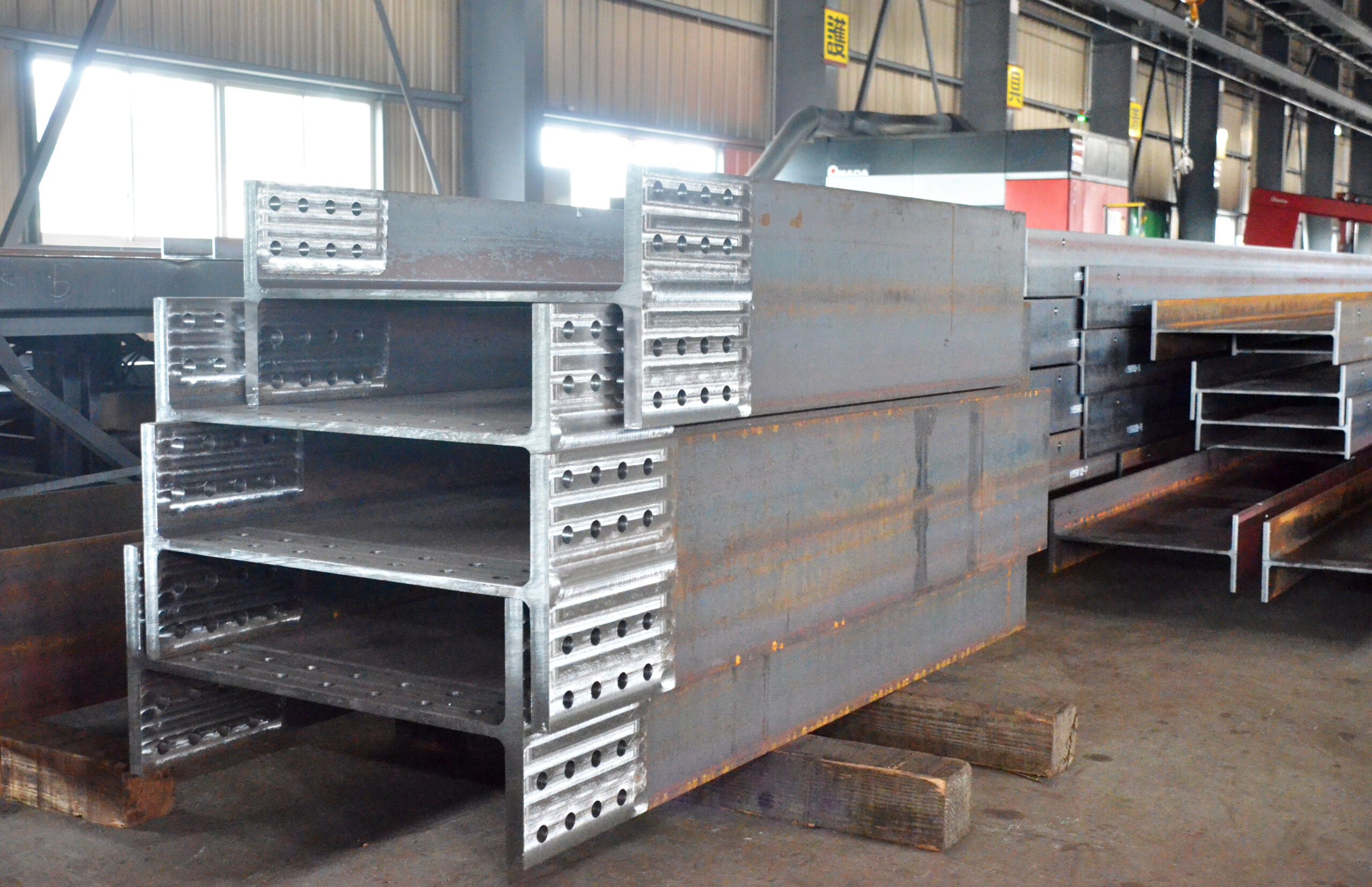
工場の至る所に加工された特殊鉄骨が出番を待っている
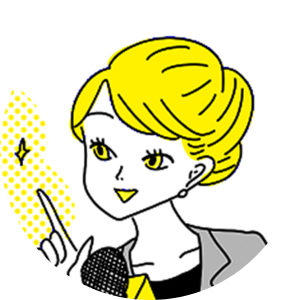
ラボ
黒瀬さんが入社されてから、北陸建工さんはすごい勢いで成長を遂げていらっしゃると思いますが、その成長のキッカケはどんなところにありますか?
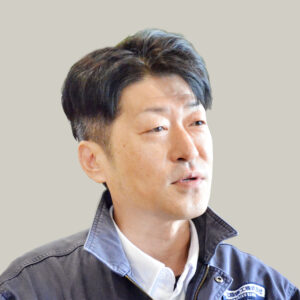
黒瀬さん
照明鉄塔や無線鉄塔で何千塔の実績を挙げ、“特殊鉄骨”をやり始めたことをきっかけに、徐々に会社の規模も大きくなっていきました。
最近では、J1リーグのサンフレッチェ広島のホームグラウンドであるエディオンピースウイング広島や駒沢オリンピック公園の特殊鉄骨の施工を担当させて頂きました。
一般的な物件は、柱や梁などの鉄骨部品にある程度共通点があり、それを使って効率化や精度確保を図るのですが、広島スタジアムは部品一つひとつが角度や長さ、厚みなど全てが違っていて共通点を見出せませんでした。
つまり、何万ピースもの“一種一品”の部品の組み合わせで、出来上がっているんです。
特に「張弦梁(ちょうげんばり)」と言って、スタジアムの端から端までの140mを張力だけで持たせた梁が有名になりましたが、個人的にはそれを支える鋼管柱製造が一番難易度が高いものだったと思います。
鉄で作ったパイプは厚みが40〜60mmあって、熱の影響で縮んだり、曲がったりします。それを予想しながら作ったり直したり、さらに何十台もある柱も一種一品…持てるもの全てを出し切りました。
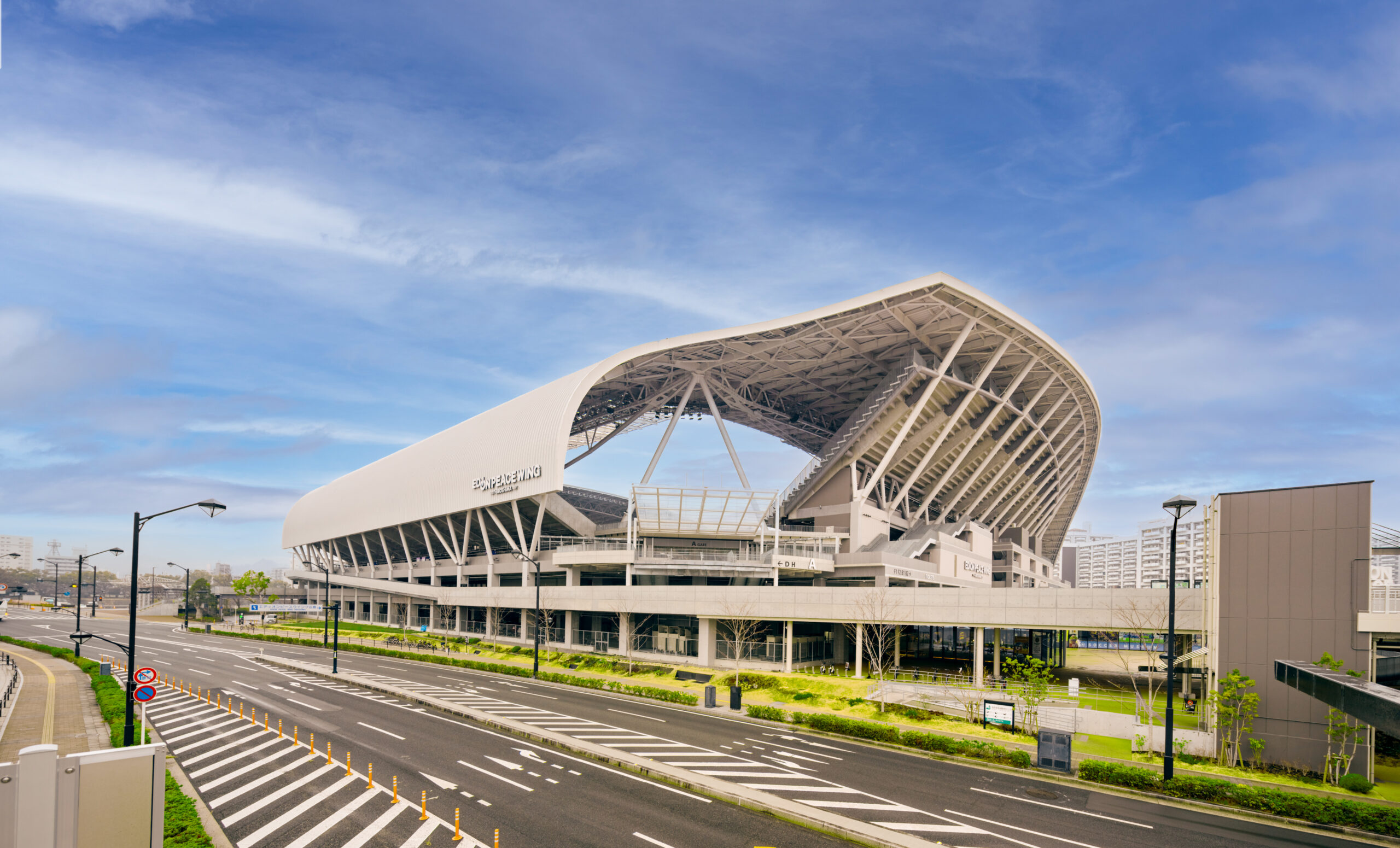
日本初のまちなかスタジアム「エディオンピースウイング広島」
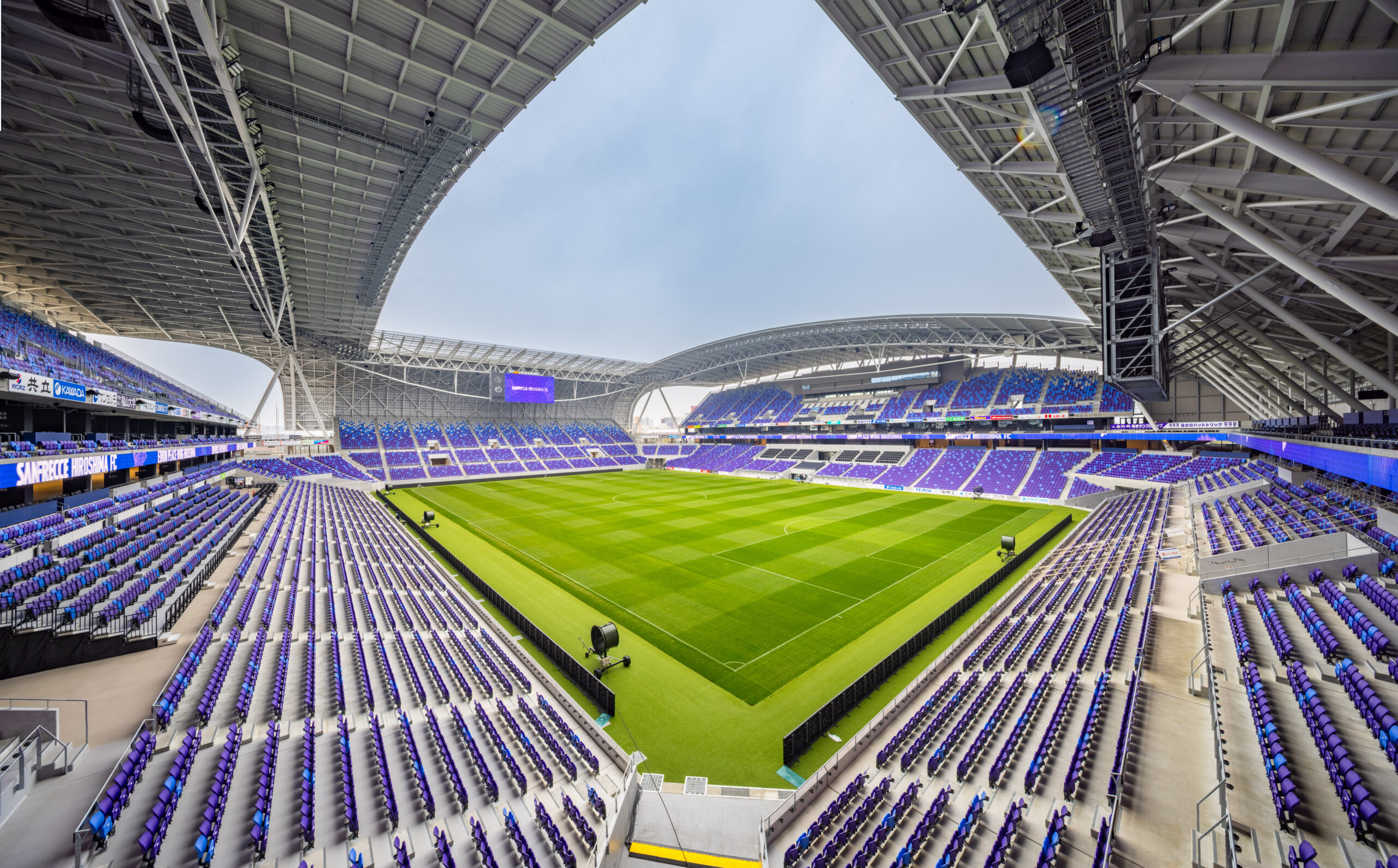
この鉄パイプ一つひとつに「技術」とその苦労が詰まっている
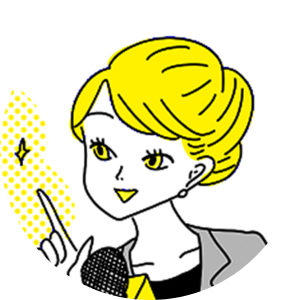
ラボ
「鉄」の分野においてここまでの技術がある会社は、全国でもなかなかないのではないでしょうか…?
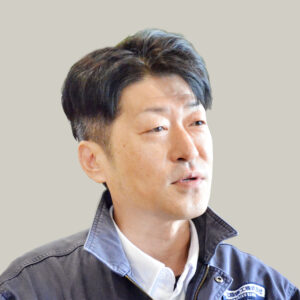
黒瀬さん
そうですね。他社では出来ないので、様々なお客様からお声掛け頂けるようになったんだと思います。
鉄骨工場の信頼度を表すグレードというものが国から定められていて、15年前くらいにM(MIddle)からH(High)になり、そこから扱える鋼材の種類や厚み、建物の大きさの幅が格段に増え、より大きな特殊鉄骨を請け負うようになりました。
「曲げ」の技術など、照明鉄塔で鍛え上げてきた技術とノウハウが、特殊鉄骨においてもかなりの武器になっています。
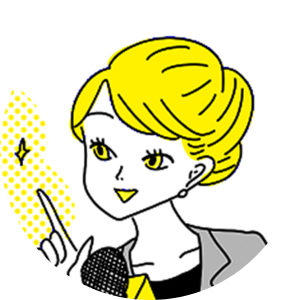
ラボ
黒瀬さんが一番大変だったお仕事をあえて挙げるとすればどうでしょうか?
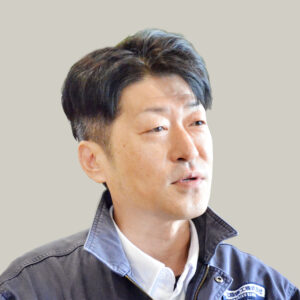
黒瀬さん
駒沢オリンピック公園のアーチ状の吊屋根を作った時ですね。短期だったこともあって、今までで一番ハードでした…。
先ほどお話しした大組み、仮組みをするべく、まず40m×40mほどのスペースに製品の実物大の原寸と治具(部品の位置出し用の道具)設置位置を手作業で書き出します。
それから設置位置レベル出しをし、治具上に部品同士を合わせていく。合わなかったらまたレベル出しをするという繰り返し。何千箇所のレベルを見たかわからないです。完成後に会社のみんなで施工ツアーに行った時は、実物を見て鳥肌が立ちましたね。
富山駅正面のローターリーの屋根や、総曲輪グランドプラザの屋根も当社で施工しています。こうした経験があるから、どんな特殊な形のオーダーが来てももう恐くはないですね。
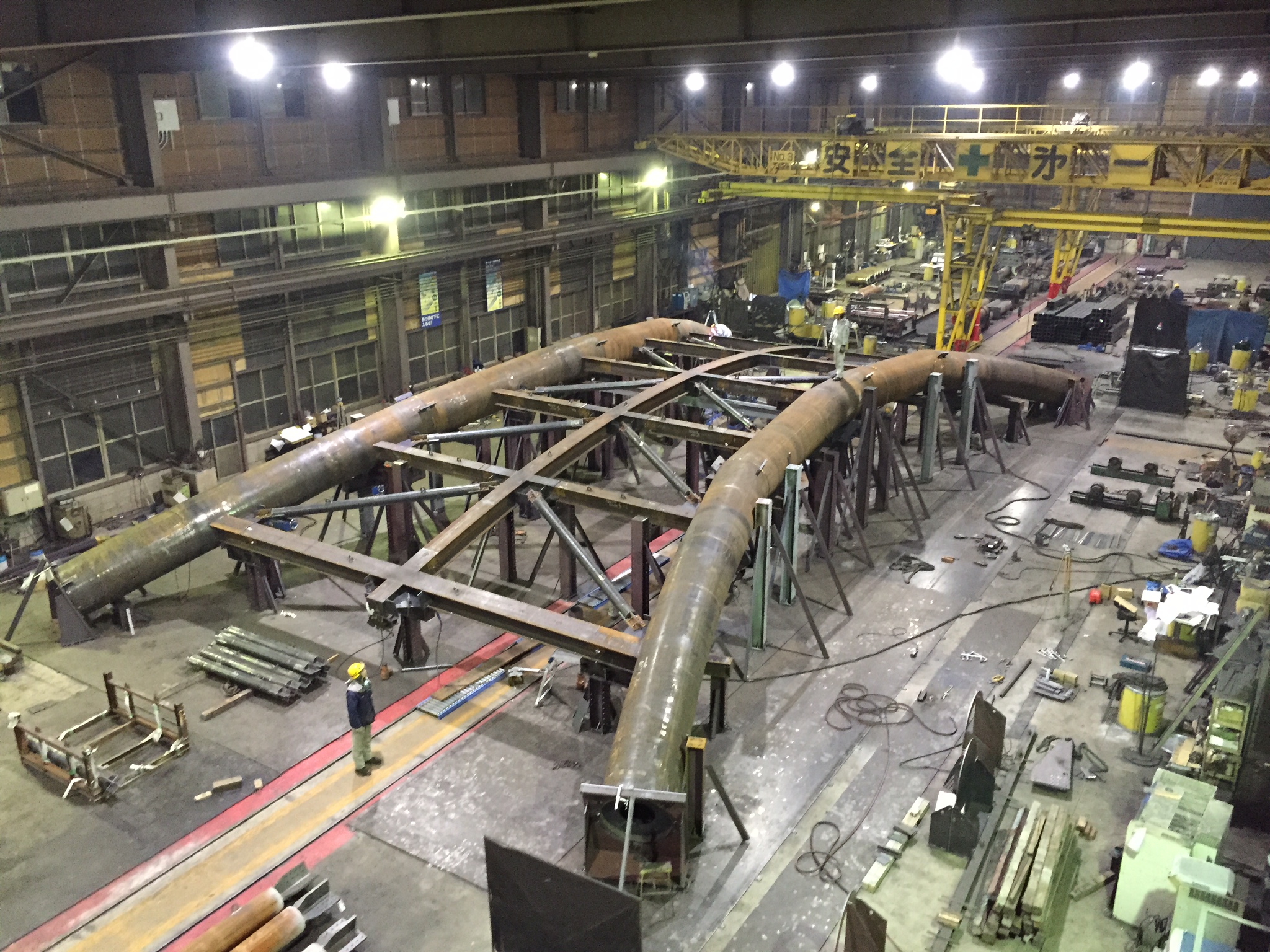
駒沢オリンピック公園の工場製作時
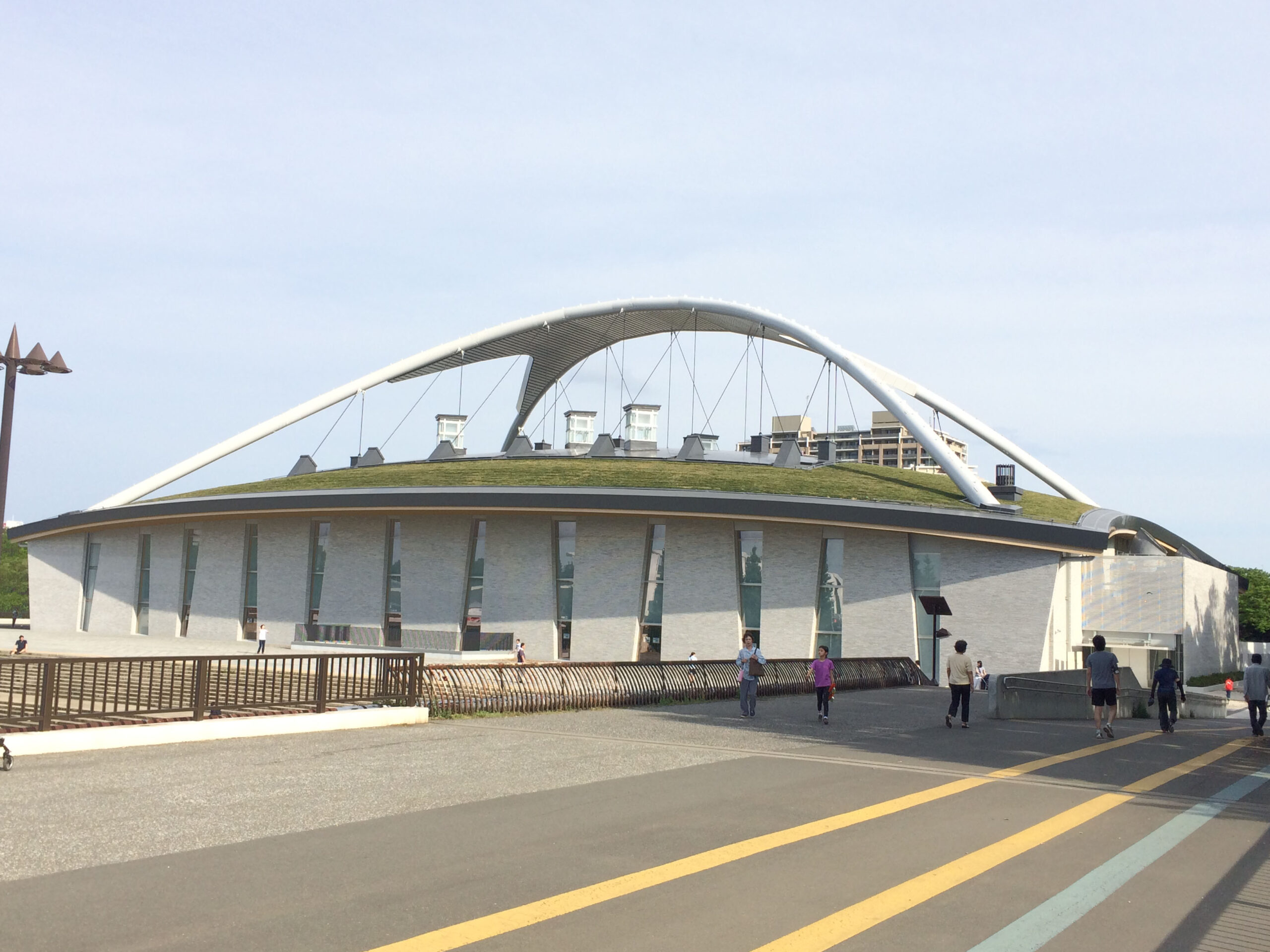
駒沢オリンピック公園総合運動場。屋内球技場のアーチ架構で下部が鉄筋コンクリート構造、ピボット支承を介してつながっている。支承間は極厚のH鋼で連結されている
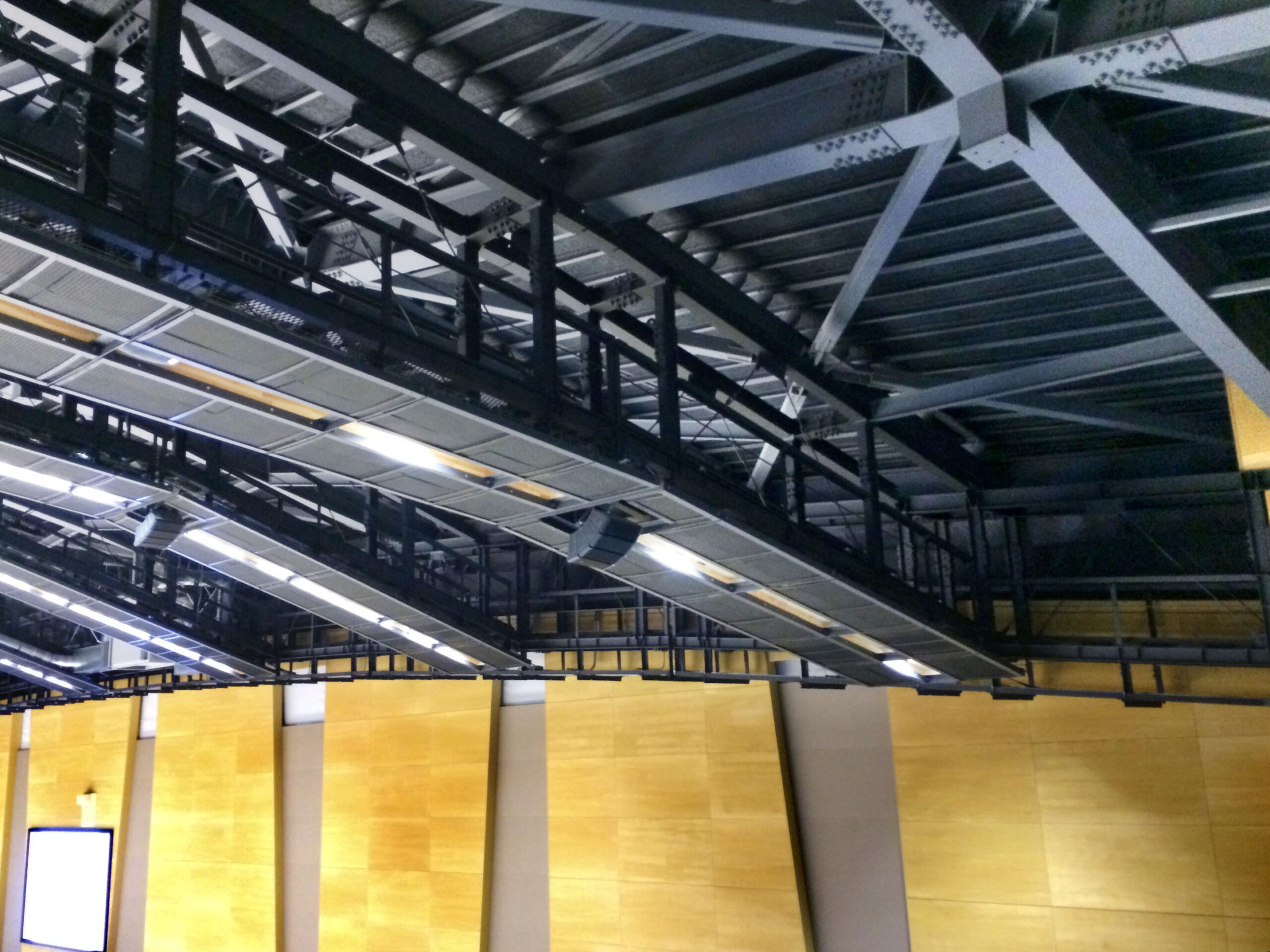
屋内運動場内の天井梁
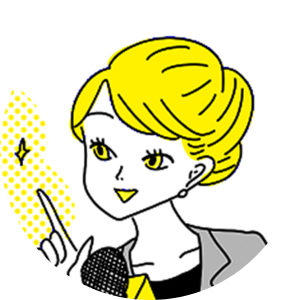
ラボ
誰もが知る建物を手掛けるというのは、大変だけどやりがいも大きいですね!
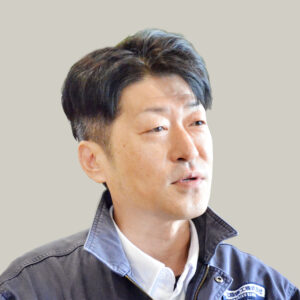
黒瀬
自分の手掛けた建物がテレビに映ったり、観光でそこを通ったりすると、すごく誇らしい気持ちになります。プレッシャーも半端じゃないけれど、それこそが規模の大きい建物を手掛ける魅力だと思います。
特殊鉄骨は流れ作業ではないオーダーメイドであるところが面白い。一つひとつ、どうやって作るか毎回新しいチャレンジができるのが、この仕事の醍醐味ですね。
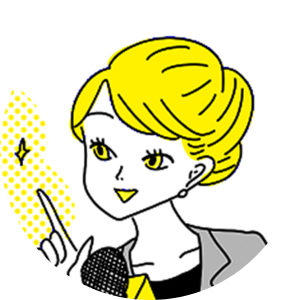
ラボ
百戦錬磨の黒瀬さんにとって、仕事をする上で「大切にしていること」は何ですか?
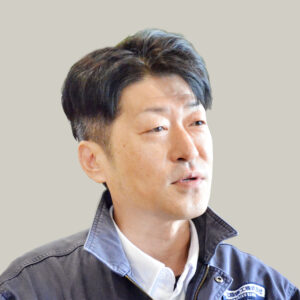
黒瀬
施工するうえで安全第一は大前提ですが、こだわっているのはやはり“精度”です。世に出して恥ずかしく無いものを作るということです。
鉄骨業界では一般的に、「3mm以内の誤差」という一般的な許容がありますが、当社は“誤差ゼロ”を心がけています。
現場施工の人たちにも、「仕事しやすい!」と思われるものを作ることが信頼に繋がるので、製造のスタッフにも精度管理を徹底するように教育しています。
部下たちには、枠を決めずに「なんでもやりなさい、いろんなことをやりなさい」と伝えています。
自分たちが経験した事のない作業や業務なども「無理だ!」と思わずにチャレンジしていこうよと。いろんな視点を持つことが、自分の力を伸ばすためにはすごく大切なことだと思います。
一つの事に特化する事も大切ですが、色んな視点を持つ事が、今後の自分の力や会社の力を伸ばすために重要な事だと考えています。
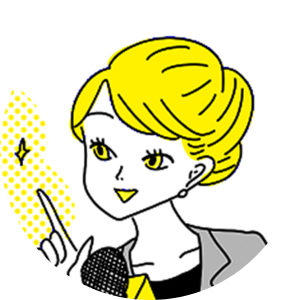
ラボ
それでは最後に、建設業を目指す若者たちにメッセージをお願いします!
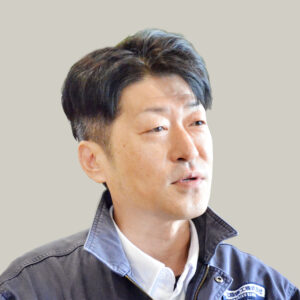
黒瀬さん
きっかけはどうであれ、長く続けること、追求することが大事です。様々な作業や業務、免許や資格、高難易度物件なども自分には絶対無理だと思っていたけど、まぁ何とかなります。
伝えたいのは「人、モノ、言葉、自分の周りの全てに対して可能性を決めつけないでほしい」ということです。
入社当時、上司に言ってもらった「この業界、やればやるほど儲かるぞ」という言葉は今でも忘れません。
進路を決めきれず、残った会社に就職し、鉄に全く興味がなかった僕が今こうして100人の部下と一緒に仕事で汗を流していられるのも、可能性を決めつけずにその言葉を信じて突き進んできたからです。この先もどんどん上を目指して頑張っていきます!